The move by Intelligent Fingerprinting comes in readiness for the commercialisation of the drug screening system.
Intelligent Fingerprinting has committed to expand R&D and manufacturing facilities and recruit additional staff since moving to new 11,000 sq ft Cambridge premises in 2015.
Over the last year the company has successfully scaled manufacturing capacity of its drug test cartridges, and considerable future scale-up will be achievable without further capital investment through the addition of more production staff.
The company said the portable system is easy-to-use, non-invasive and works in under 10 minutes by analysing the tiny traces of sweat contained in a fingerprint. With appropriate regulatory approval, it can be used in various environments to support a range of applications including police initiatives and coroner services, as well as establishing fitness for duty in safety critical workplaces.
“Our Cambridge HQ facility was designed from the outset for high throughput manufacturing, and we now have a first phase operation in place that can support production requirements following commercialisation,” said Dr Jerry Walker, chief executive of Intelligent Fingerprinting.
“Additionally, following our recent announcement of a further £3 million of funding, we’re in a position to introduce further production and automated assembly enhancements as we scale our manufacturing to commercial volumes and reduce unit costs.”
Firm scales manufacturing capacity 10-fold
A Cambridge-based company, which is developing a portable fingerprint-based drug screening system, has scaled its manufacturing capacity 10-fold over the last year.
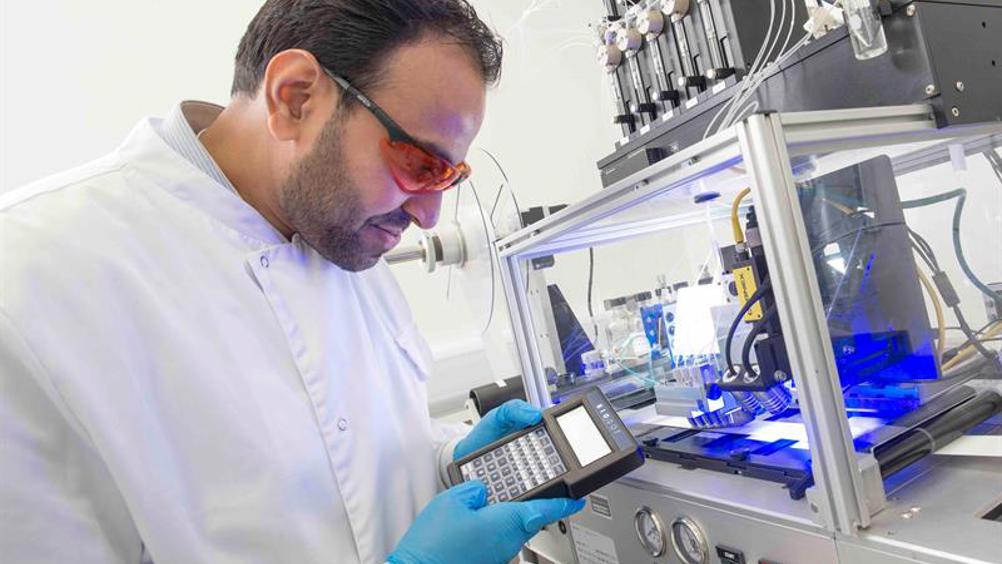